Fotoresistin päällystysmenetelmät jaetaan yleensä spin-, kasto- ja telapinnoitusmenetelmiin, joista spincoating on yleisimmin käytetty. Spin-pinnoituksella fotoresisti tippuu substraatille, ja alustaa voidaan pyörittää suurella nopeudella fotoresistikalvon saamiseksi. Sen jälkeen voidaan saada kiinteä kalvo kuumentamalla sitä keittolevyllä. Spin coating soveltuu päällystämiseen ultraohuista kalvoista (noin 20nm) paksuihin noin 100um kalvoihin. Sen ominaisuudet ovat hyvä tasaisuus, tasainen kalvon paksuus kiekkojen välillä, vähän vikoja jne., ja voidaan saada kalvo, jolla on korkea pinnoituskyky.
Spin-pinnoitusprosessi
Spin-pinnoituksen aikana substraatin pääkiertonopeus määrää fotoresistin kalvon paksuuden. Pyörimisnopeuden ja kalvon paksuuden välinen suhde on seuraava:
Spin = kTn
Kaavassa Spin on pyörimisnopeus; T on kalvon paksuus; k ja n ovat vakioita.
Spin-pinnoitusprosessiin vaikuttavat tekijät
Vaikka kalvon paksuus määräytyy pääpyörimisnopeuden mukaan, se liittyy myös huoneen lämpötilaan, kosteuteen, fotoresistin viskositeettiin ja fotoresistin tyyppiin. Eri tyyppisten fotoresistipinnoituskäyrien vertailu on esitetty kuvassa 1.
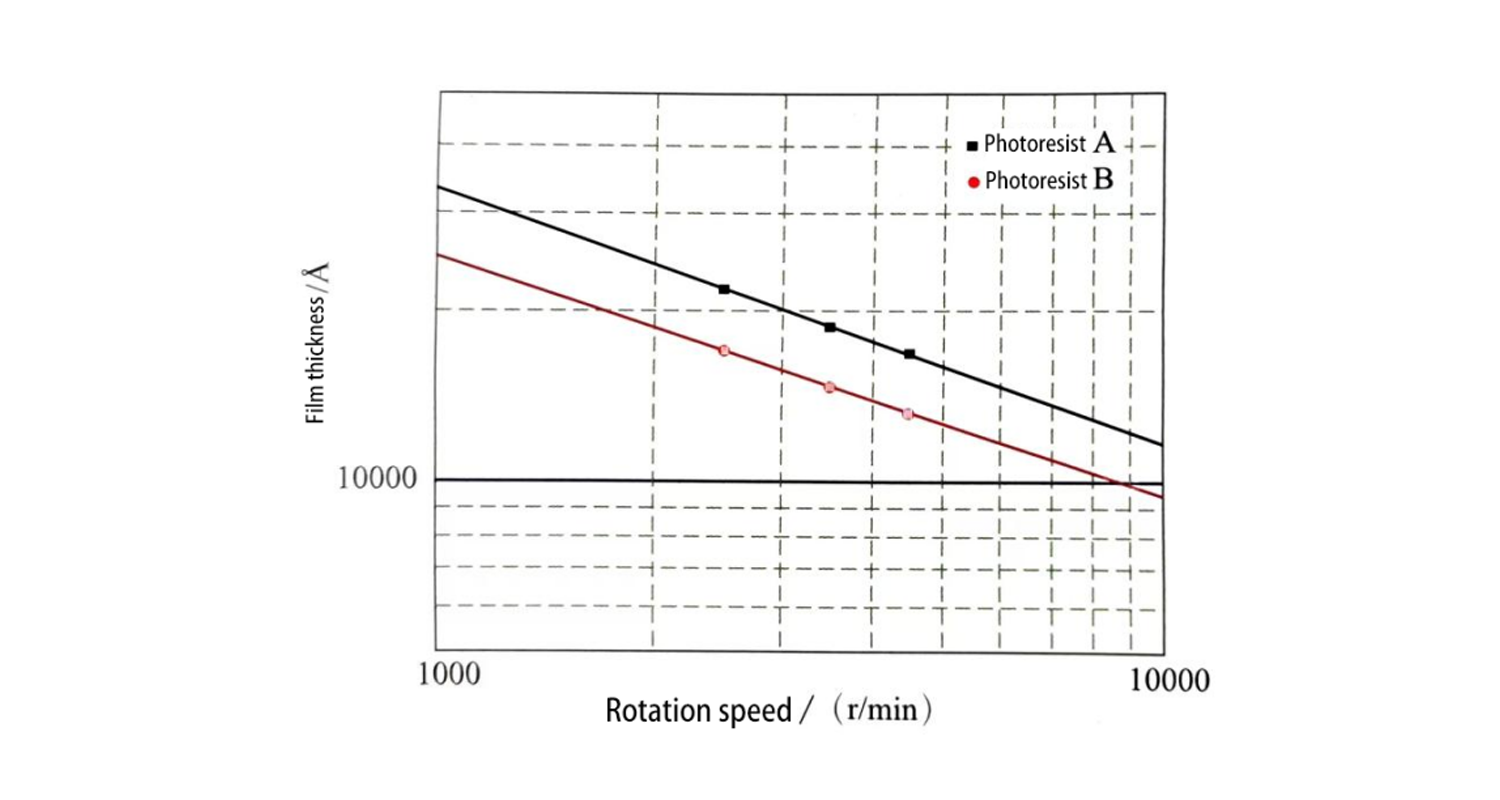
Kuva 1: Erityyppisten fotoresistipinnoituskäyrien vertailu
Pääkiertoajan vaikutus
Mitä lyhyempi pääkiertoaika, sitä paksumpi kalvon paksuus. Kun pääkiertoaikaa pidennetään, sitä ohuemmaksi kalvo tulee. Kun se ylittää 20s, kalvon paksuus pysyy lähes muuttumattomana. Siksi pääkiertoajaksi valitaan yleensä yli 20 sekuntia. Pääkiertoajan ja kalvon paksuuden välinen suhde on esitetty kuvassa 2.
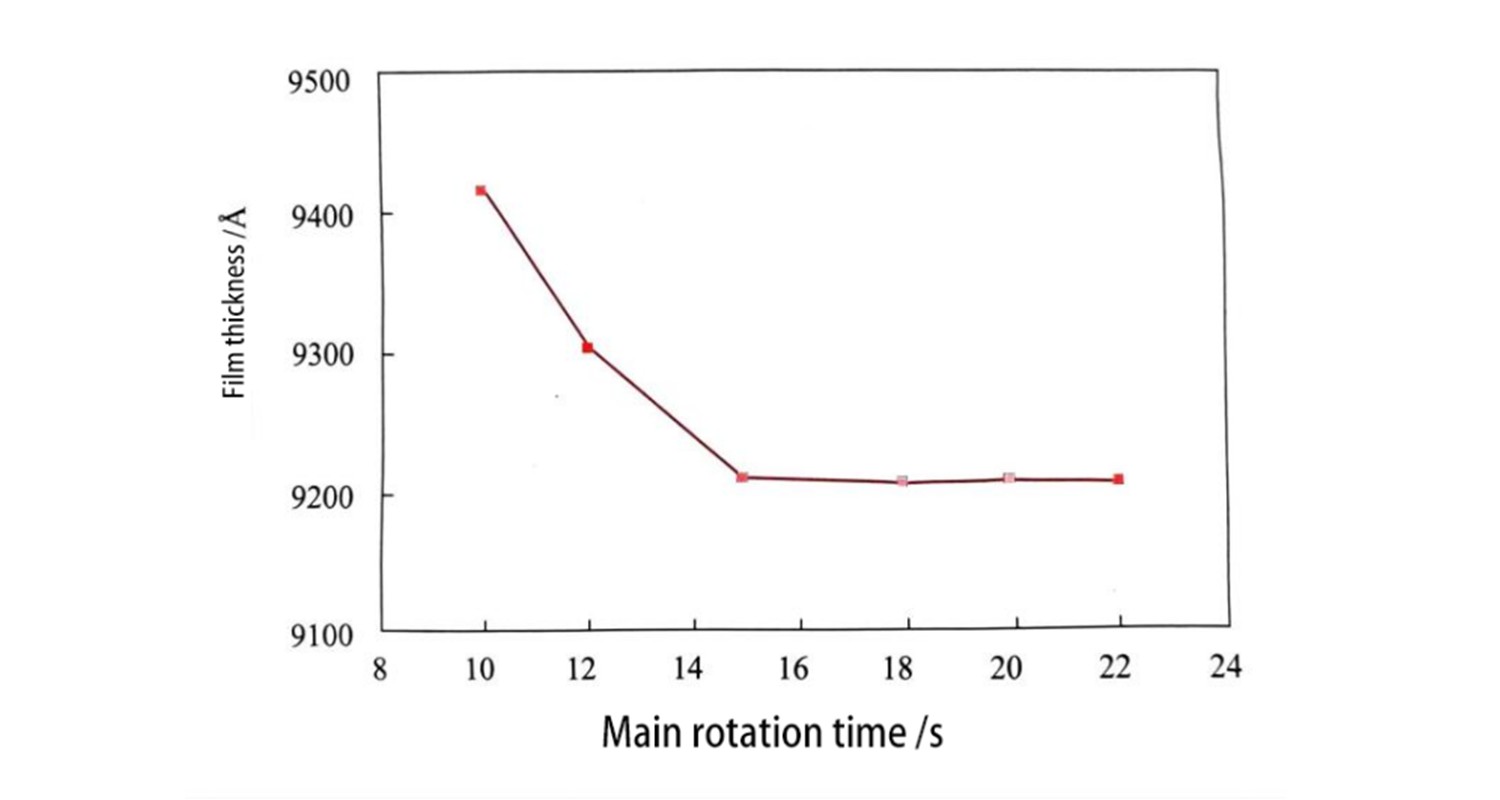
Kuva 2: Pääkiertoajan ja kalvon paksuuden välinen suhde
Kun fotoresisti tiputetaan alustalle, vaikka seuraava pääpyörimisnopeus olisi sama, substraatin pyörimisnopeus tippumisen aikana vaikuttaa lopulliseen kalvonpaksuuteen. Fotoresistikalvon paksuus kasvaa substraatin pyörimisnopeuden kasvaessa tippumisen aikana, mikä johtuu liuottimen haihtumisen vaikutuksesta, kun fotoresisti avataan tippumisen jälkeen. Kuvassa 3 on esitetty kalvon paksuuden ja pääpyörimisnopeuden välinen suhde eri substraatin pyörimisnopeuksilla fotoresistin tippumisen aikana. Kuvasta näkyy, että tippuvan substraatin pyörimisnopeuden kasvaessa kalvon paksuus muuttuu nopeammin ja ero on selvempi alueella, jossa pääpyörimisnopeus on pienempi.
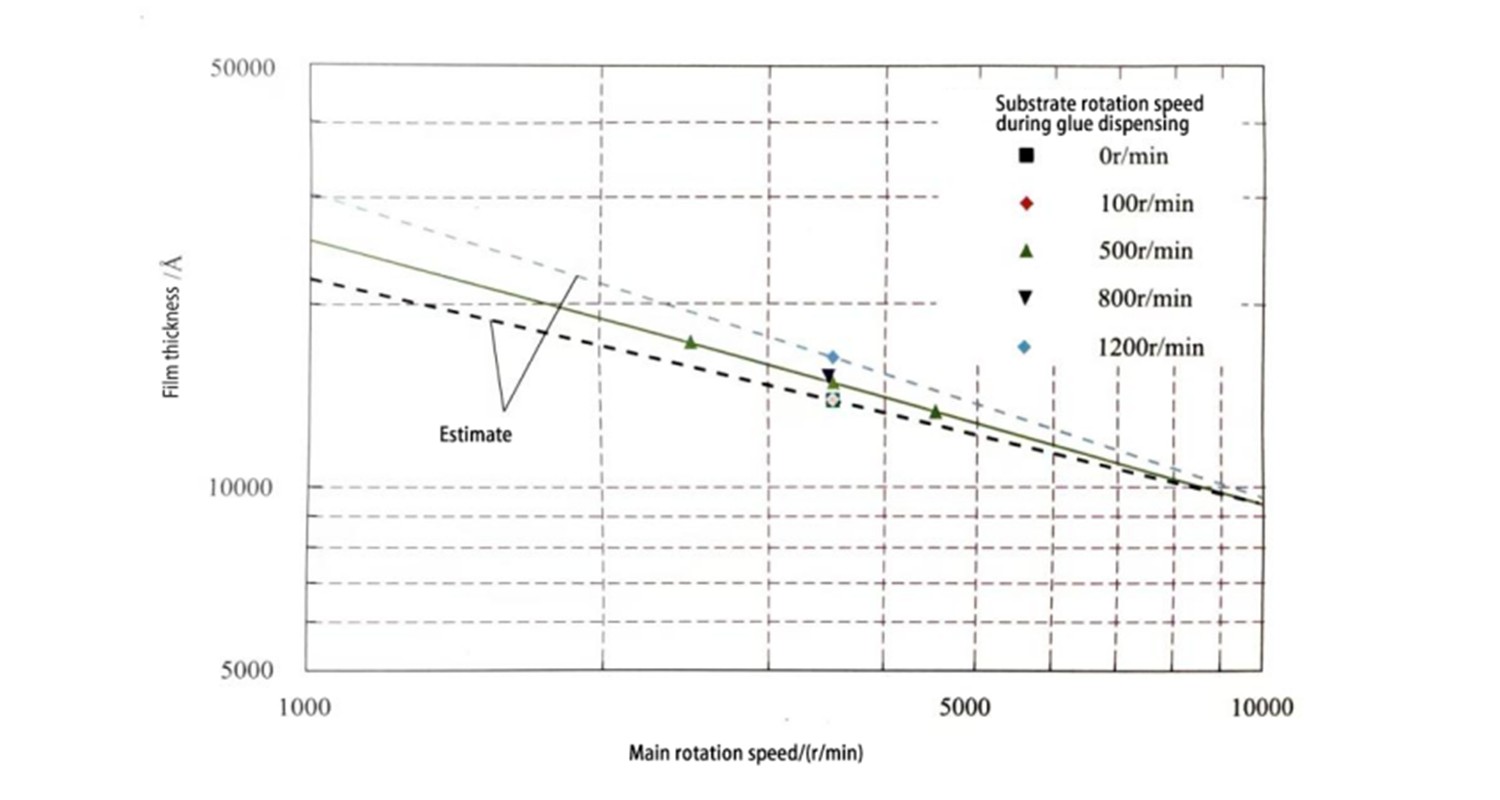
Kuva 3: Kalvon paksuuden ja pääpyörimisnopeuden välinen suhde substraatin eri pyörimisnopeuksilla fotoresistin annostelun aikana
Kosteuden vaikutus pinnoituksen aikana
Kun kosteus laskee, kalvon paksuus kasvaa, koska kosteuden väheneminen edistää liuottimen haihtumista. Kalvon paksuusjakauma ei kuitenkaan muutu merkittävästi. Kuva 4 esittää kosteuden ja kalvon paksuuden jakautumisen välistä suhdetta pinnoituksen aikana.
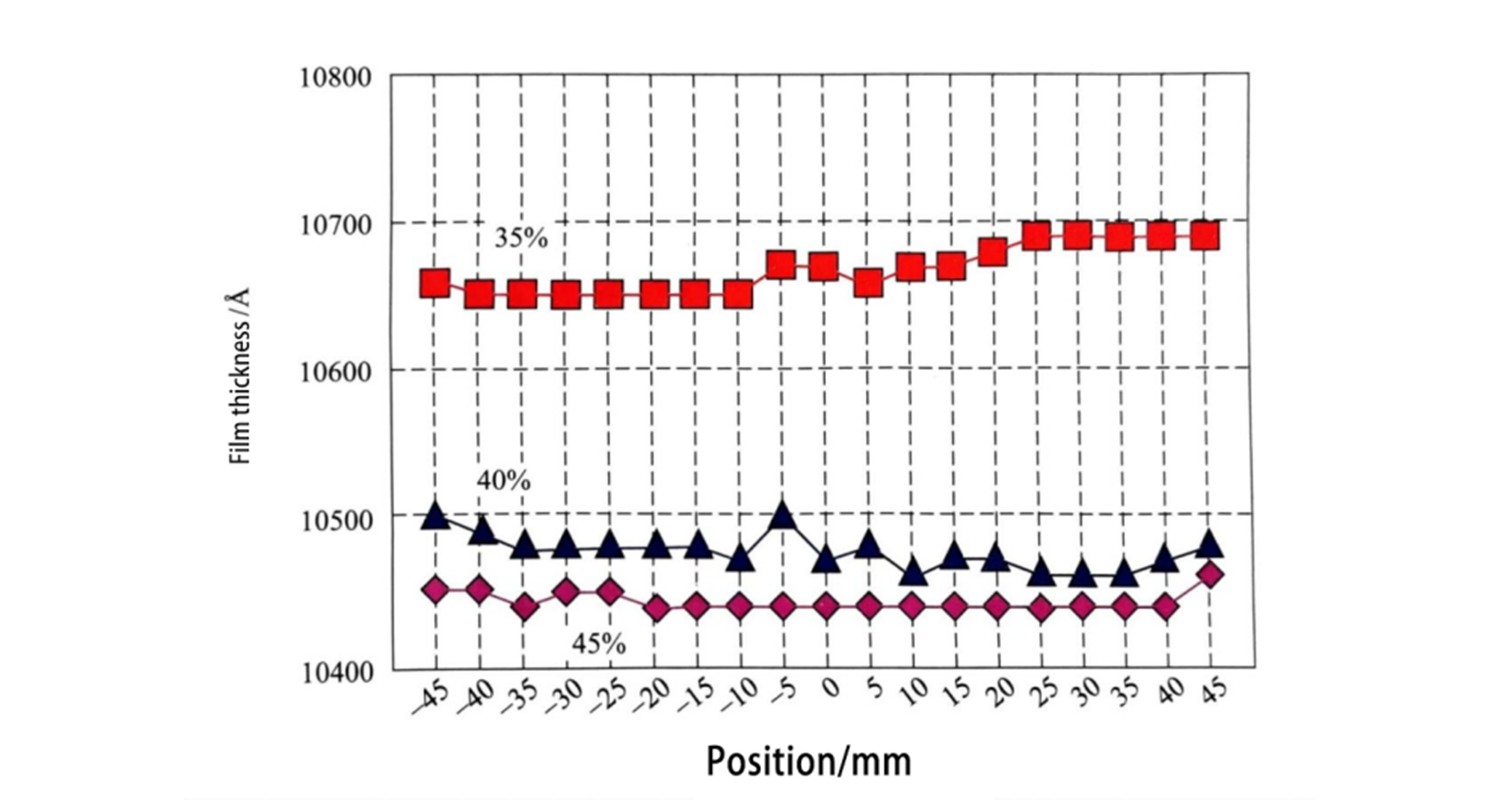
Kuva 4: Kosteuden ja kalvon paksuuden jakautumisen välinen suhde pinnoituksen aikana
Lämpötilan vaikutus pinnoituksen aikana
Kun sisälämpötila nousee, kalvon paksuus kasvaa. Kuvasta 5 voidaan nähdä, että fotoresistikalvon paksuusjakauma muuttuu kuperasta koveraksi. Kuvan käyrä osoittaa myös, että suurin tasaisuus saadaan, kun sisälämpötila on 26°C ja fotoresistin lämpötila on 21°C.
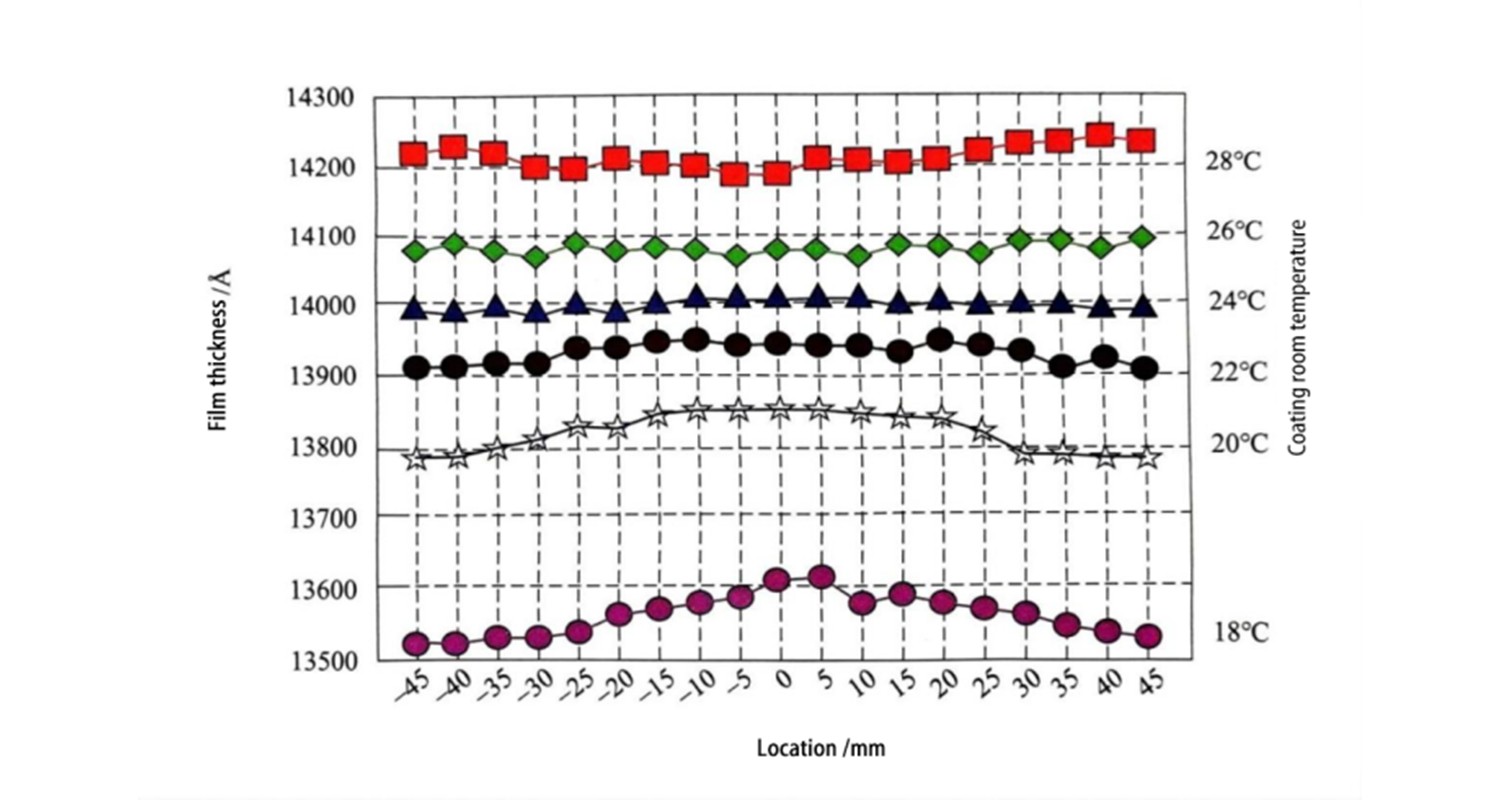
Kuva 5: Lämpötilan ja kalvon paksuuden jakautumisen välinen suhde pinnoituksen aikana
Pakokaasunopeuden vaikutus pinnoituksen aikana
Kuva 6 esittää pakokaasunopeuden ja kalvon paksuuden jakautumisen välistä suhdetta. Pakokaasun puuttuessa se osoittaa, että kiekon keskustalla on taipumus paksuuntua. Pakokaasun nopeuden lisääminen parantaa tasaisuutta, mutta jos sitä lisätään liikaa, tasaisuus vähenee. Voidaan nähdä, että pakokaasunopeudelle on optimaalinen arvo.
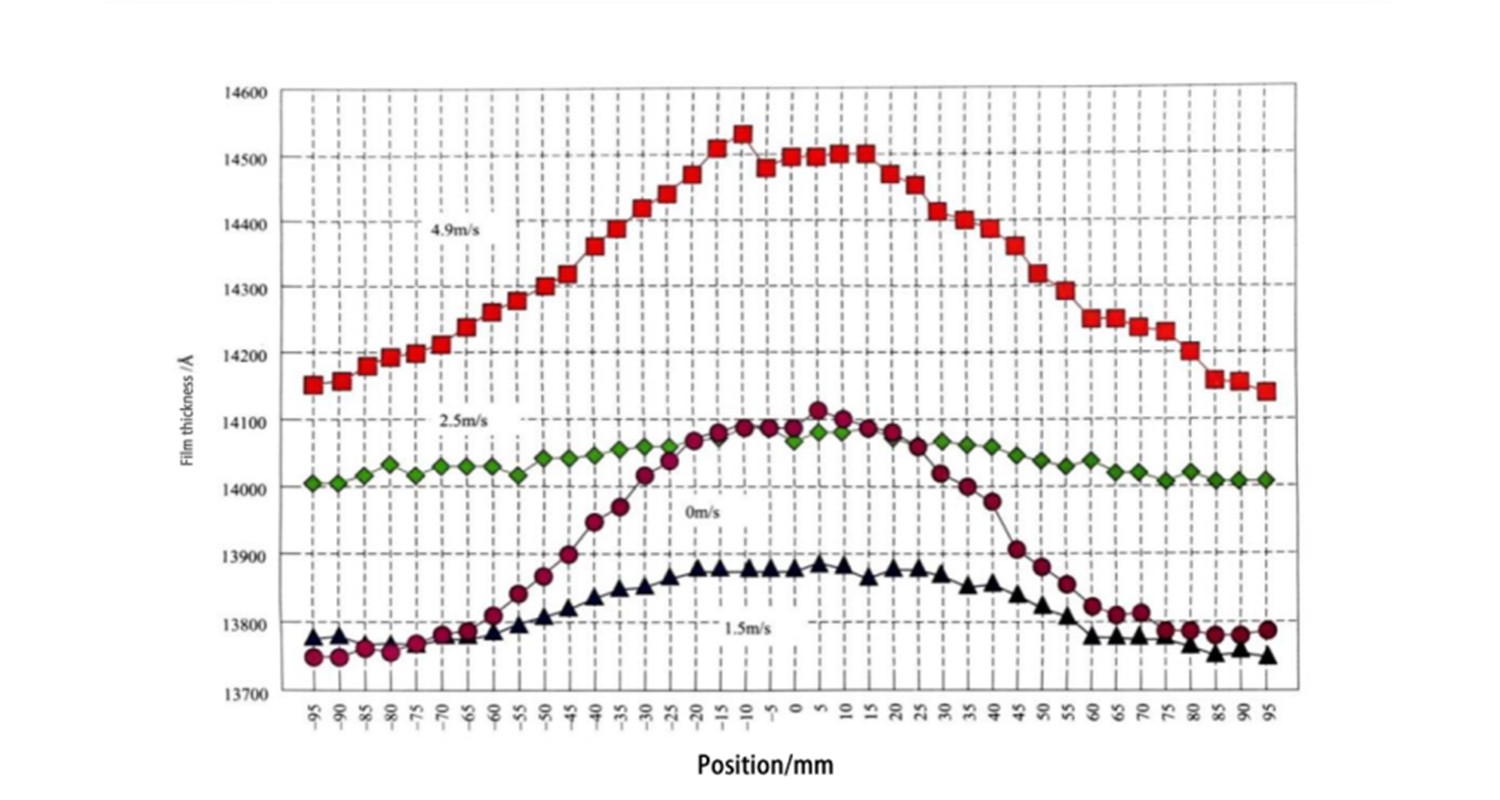
Kuva 6: Pakokaasunopeuden ja kalvon paksuuden jakautumisen välinen suhde
HMDS-hoito
Jotta fotoresisti olisi päällystettävämpi, kiekko on käsiteltävä heksametyylidisilatsaanilla (HMDS). Varsinkin kun kosteutta kiinnittyy Si-oksidikalvon pintaan, muodostuu silanolia, joka vähentää fotoresistin tarttuvuutta. Kosteuden poistamiseksi ja silanolin hajottamiseksi kiekko kuumennetaan yleensä 100-120 °C:seen ja siihen lisätään HMDS-sumua kemiallisen reaktion aiheuttamiseksi. Reaktiomekanismi on esitetty kuvassa 7. HMDS-käsittelyn avulla hydrofiilisesta pinnasta, jolla on pieni kosketuskulma, tulee hydrofobinen pinta, jolla on suuri kosketuskulma. Kiekon kuumentaminen voi saavuttaa paremman fotoresistin tarttuvuuden.
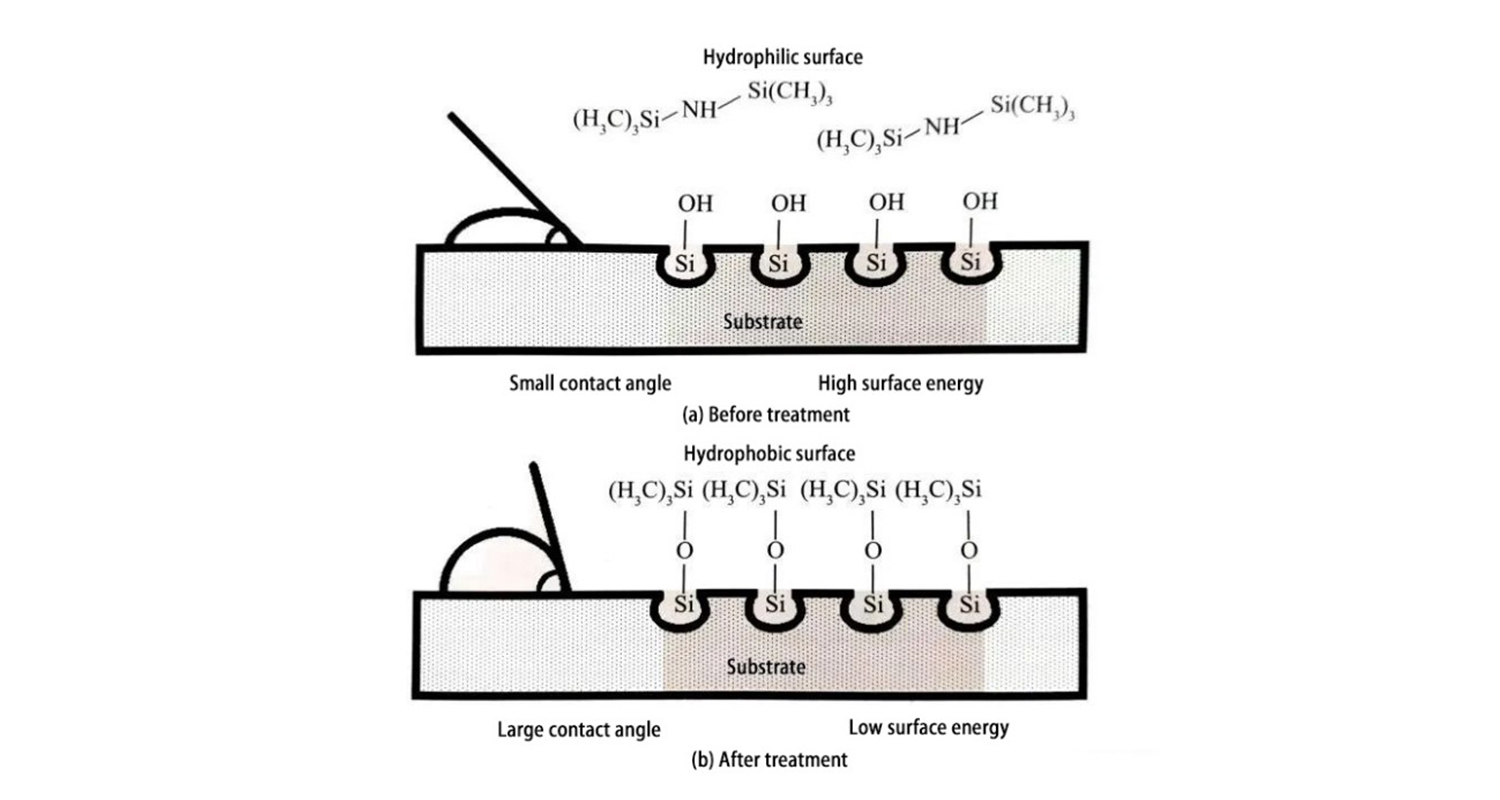
Kuva 7: HMDS-reaktiomekanismi
HMDS-hoidon vaikutus voidaan havaita mittaamalla kosketuskulma. Kuvassa 8 on esitetty HMDS-käsittelyajan ja kosketuskulman välinen suhde (käsittelylämpötila 110 °C). Substraatti on Si, HMDS-käsittelyaika on yli 1 min, kosketuskulma on suurempi kuin 80 ° ja käsittelyvaikutus on vakaa. Kuvassa 9 on esitetty HMDS-käsittelylämpötilan ja kosketuskulman välinen suhde (käsittelyaika 60 s). Kun lämpötila ylittää 120 ℃, kosketuskulma pienenee, mikä osoittaa, että HMDS hajoaa lämmön vaikutuksesta. Siksi HMDS-käsittely suoritetaan yleensä 100-110 ℃:ssa.
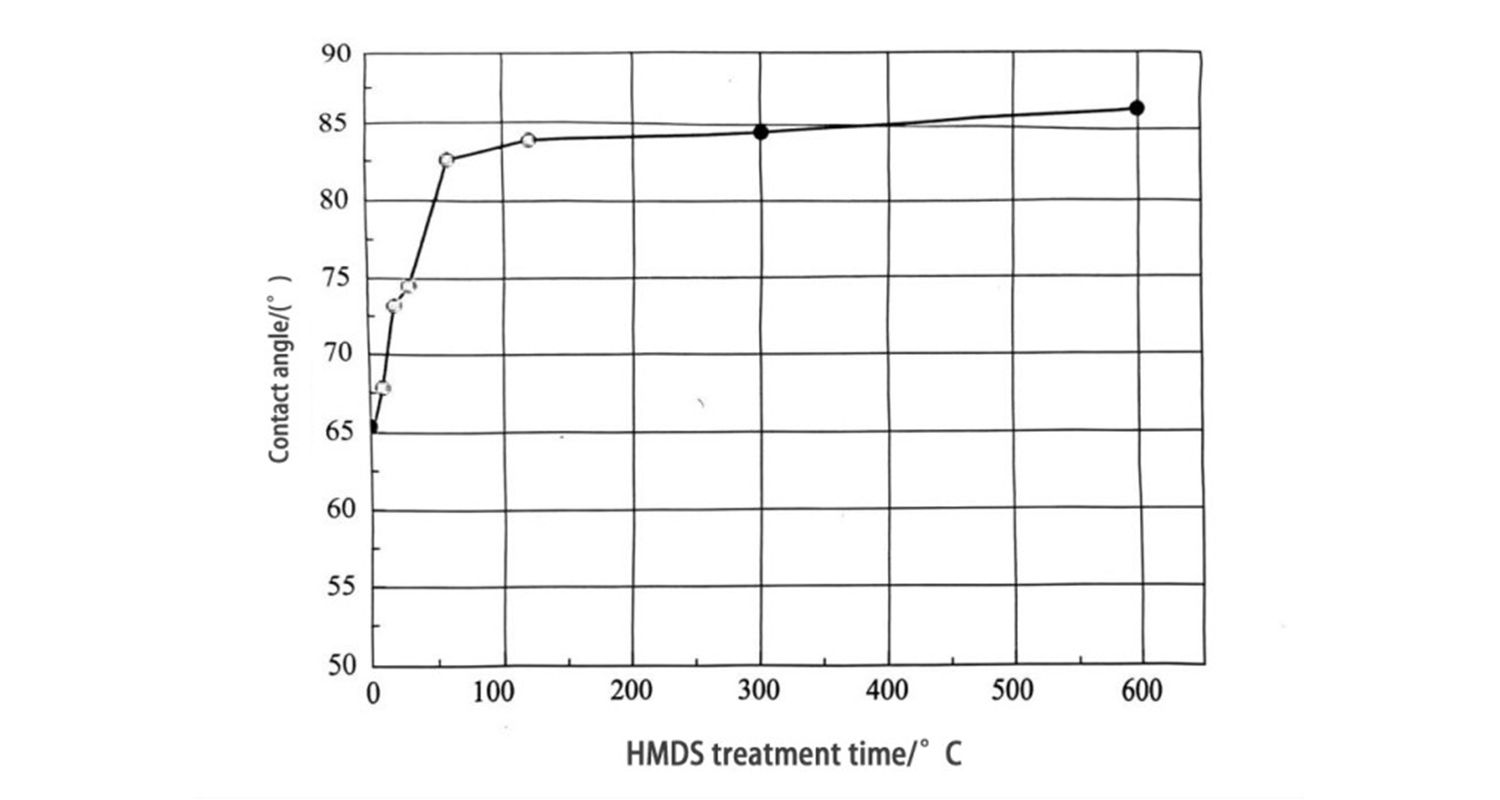
Kuva 8: HMDS-hoitoajan välinen suhde
ja kosketuskulma (käsittelylämpötila 110 ℃)
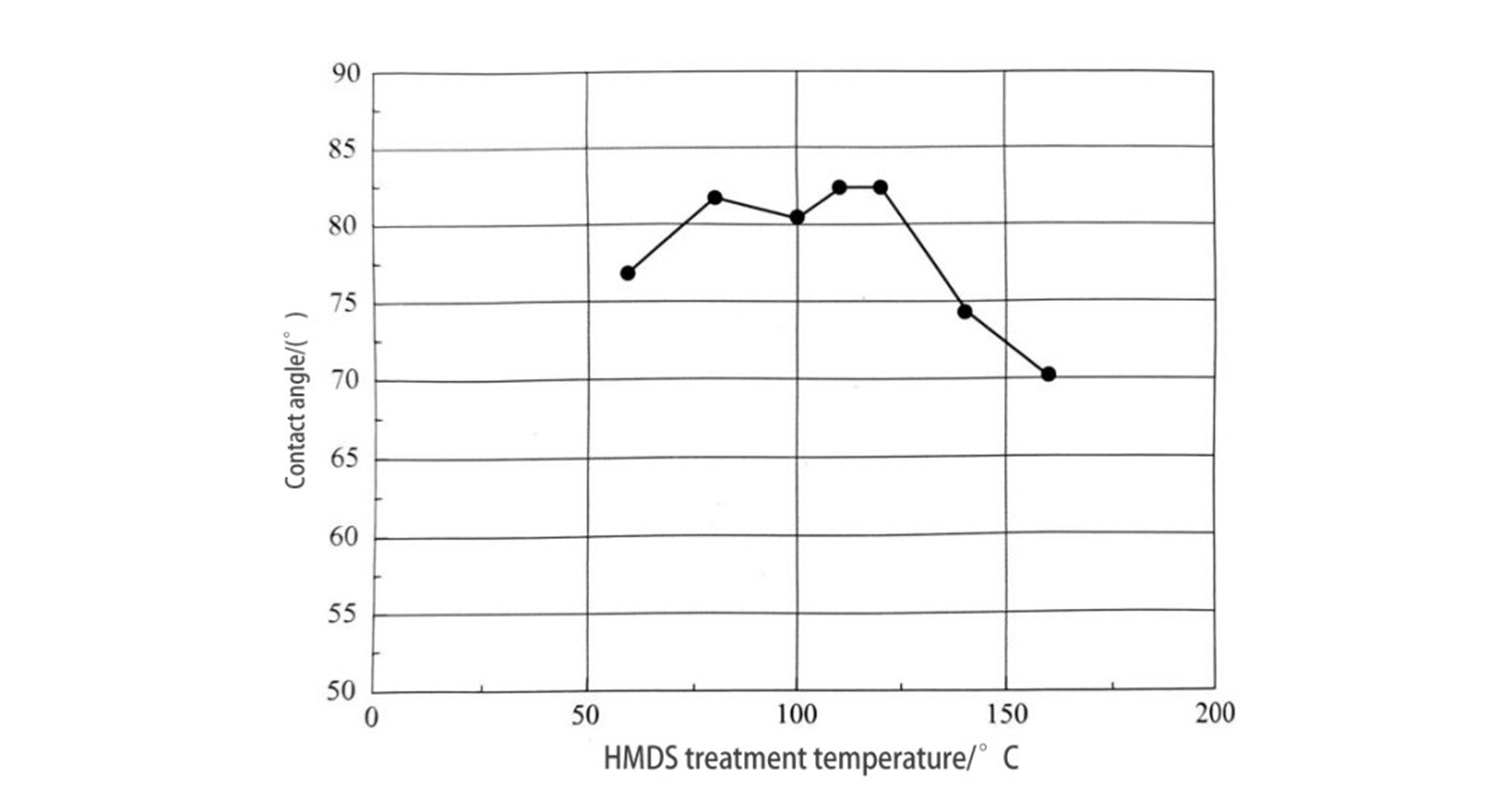
Kuva 9: HMDS-käsittelyn lämpötilan ja kosketuskulman välinen suhde (hoitoaika 60 s)
HMDS-käsittely suoritetaan piisubstraatille, jossa on oksidikalvo fotoresistikuvion muodostamiseksi. Oksidikalvo syövytetään sitten fluorivetyhapolla, johon on lisätty puskuria, ja havaitaan, että HMDS-käsittelyn jälkeen fotoresistikuvio voidaan estää putoamasta. Kuvio 10 esittää HMDS-käsittelyn vaikutuksen (kuvion koko on 1 um).
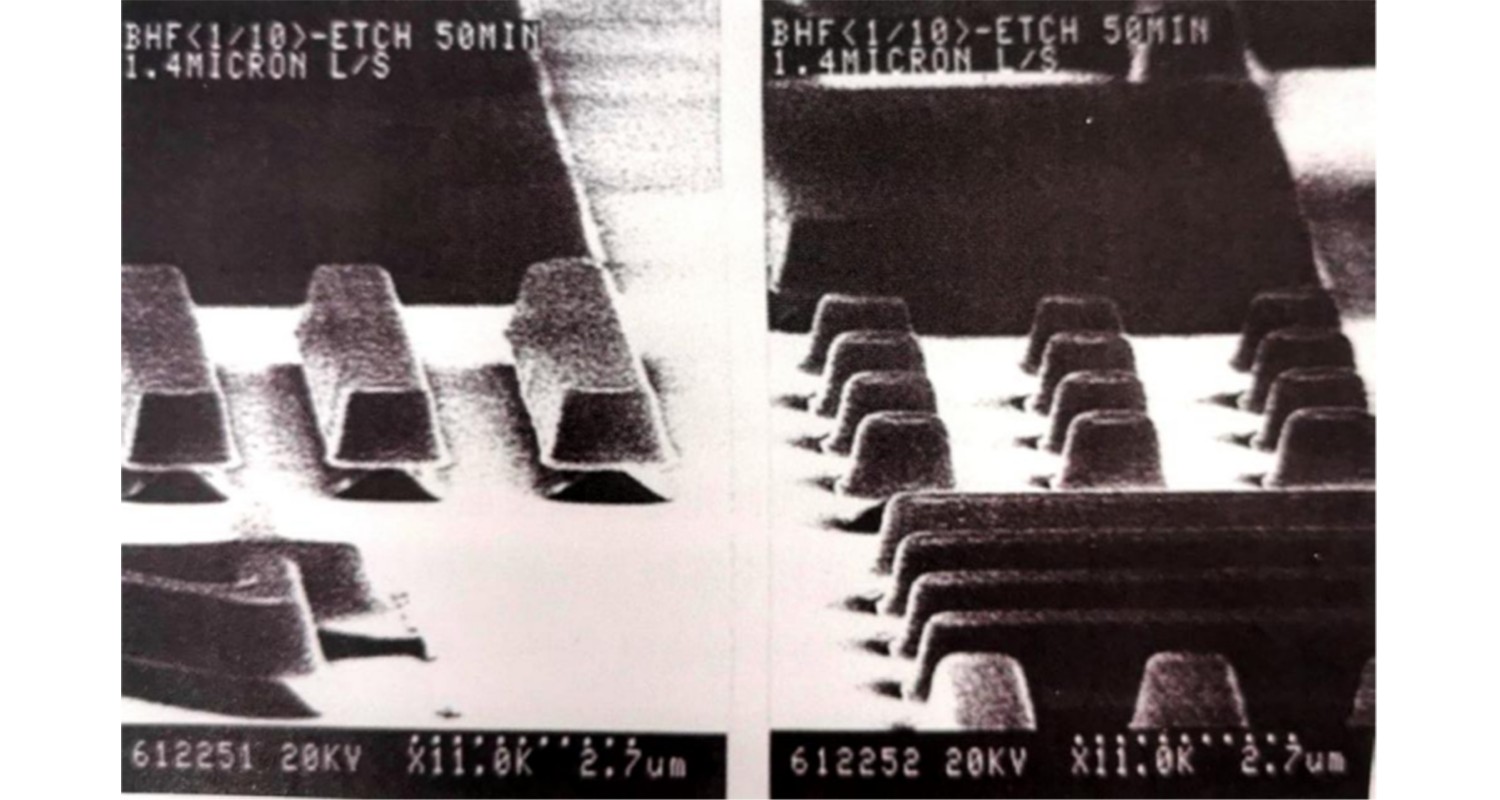
Kuva 10: HMDS-hoidon vaikutus (kuvion koko on 1 um)
Esipaistaminen
Samalla pyörimisnopeudella, mitä korkeampi esipaistolämpötila, sitä pienempi kalvon paksuus, mikä osoittaa, että mitä korkeampi esipaistolämpötila, sitä enemmän liuotinta haihtuu, mikä johtaa ohuempaan kalvonpaksuuteen. Kuva 11 esittää esipaistolämpötilan ja Dill's A -parametrin välisen suhteen. A-parametri ilmaisee valoherkän aineen pitoisuuden. Kuten kuvasta voidaan nähdä, kun esipaistolämpötila nousee yli 140°C, A-parametri laskee, mikä osoittaa, että valoherkkä aine hajoaa tätä korkeammassa lämpötilassa. Kuva 12 esittää spektrin läpäisykykyä eri esipaistolämpötiloissa. 160°C:ssa ja 180°C:ssa voidaan havaita läpäisykyvyn kasvua aallonpituusalueella 300-500 nm. Tämä vahvistaa, että valoherkkä aine kypsyy ja hajoaa korkeissa lämpötiloissa. Esipaistolämpötilalla on optimaalinen arvo, jonka määräävät valoominaisuudet ja herkkyys.
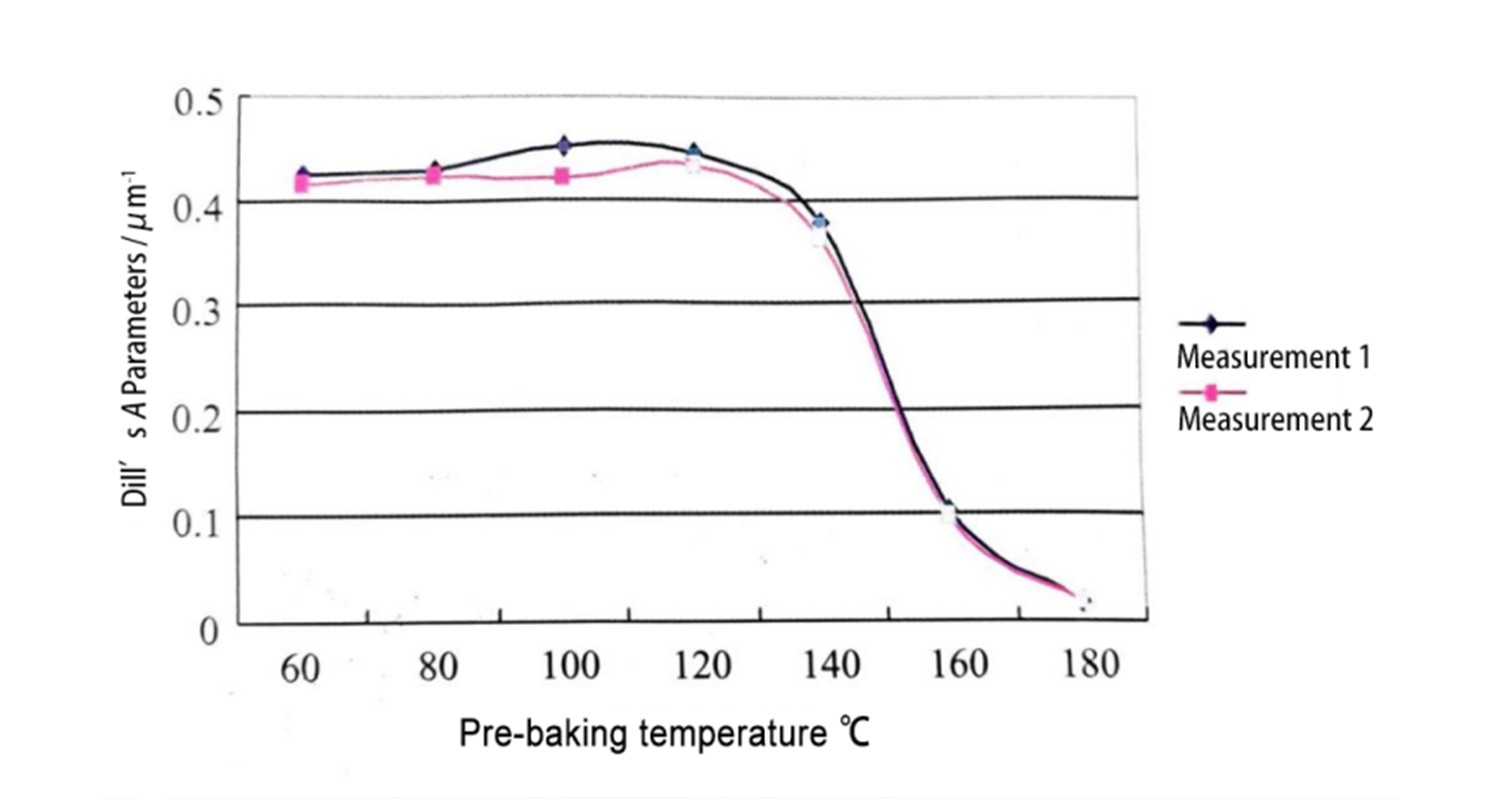
Kuva 11: Esipaistolämpötilan ja Dill's A -parametrin välinen suhde
(OFPR-800/2:n mitattu arvo)
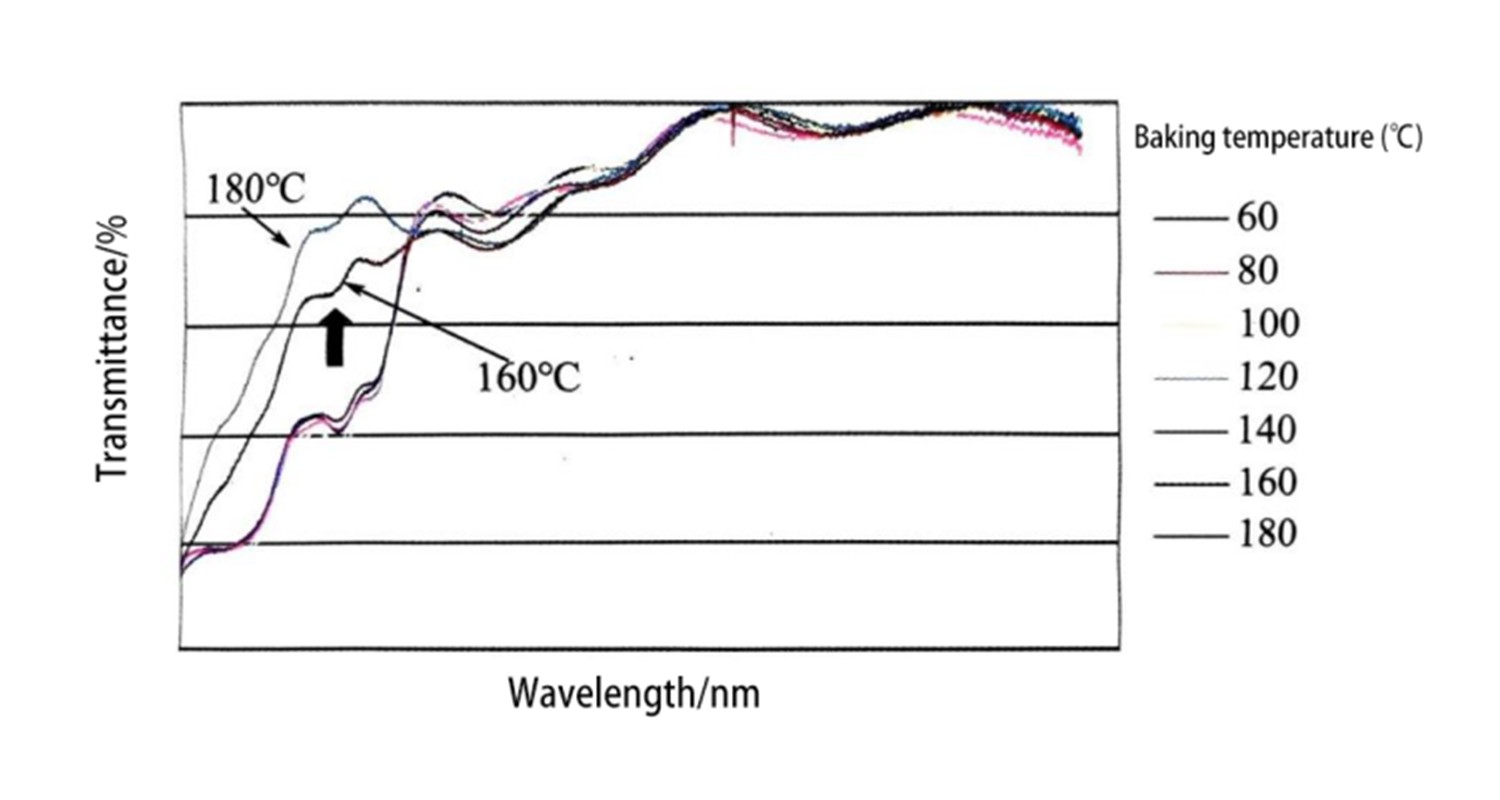
Kuva 12: Spektriläpäisevyys eri esipaistolämpötiloissa
(OFPR-800, kalvon paksuus 1um)
Lyhyesti sanottuna kehruupinnoitusmenetelmällä on ainutlaatuisia etuja, kuten kalvon paksuuden tarkka hallinta, korkea kustannustehokkuus, miedot prosessiolosuhteet ja yksinkertainen toiminta, joten sillä on merkittäviä vaikutuksia saastumisen vähentämisessä, energiansäästössä ja kustannustehokkuuden parantamisessa. Viime vuosina kehruupinnoitus on saanut yhä enemmän huomiota, ja sen käyttö on vähitellen levinnyt eri aloille.
Postitusaika: 27.11.2024